// BW-Elektrolyse 04/2020-04/2023
Der Fokus der Forschungs- und Entwicklungsarbeiten im Projekt "BW-Elektrolyse" (15.4.2020 bis 30.4.2023) lag auf einer verbesserten, einfach skalierbaren Architektur des Elektrolysesystems sowie auf Innovationen hinsichtlich des Elektrolysestacks. Dafür entwickelte das ZSW in Stuttgart eine innovative Systemtechnik nach dem Baukastenprinzip mit einer verbesserten Anlagenautomatisierung, die als Systemdemonstrator „made in Baden-Württemberg“umgesetzt wurde und als Schaufenster der Wertschöpfungspotenziale im Land einem breiten Publikum vorgestellt wurde.
Ebenso wichtig war die Entwicklung eines fortschrittlichen Elektrolysestackdesigns, das sich hinsichtlich Skalierbarkeit und Montagefreundlichkeit auszeichnet. Das Hahn-Schickard Institut in Stuttgart erforscht die Integration von Mikrosensorik in den Elektrolysestack, um Temperaturen und Zellspannung in der Elektrolysezelle am Ort der Gasentstehung zu messen und so mithilfe einer Messelektronik eventuelle Störungen frühzeitig erkennen zu können. Das Deutsche Zentrum für Luft- und Raumfahrt in Stuttgart (DLR) konzentriert sich auf die Herstellung katalytisch aktiver Beschichtungen der Elektroden durch das atmosphärische Plasmaspritzverfahren, mit denen die Zellspannung reduziert werden konnte. Die Deutschen Institute für Textil- und Faserforschung (DITF) aus Denkendorf entwickeln verbesserte, faserverstärkte Membranmaterialien, die dünn und somit effizient, aber gleichzeitig auch robust und somit langzeitstabil sind.
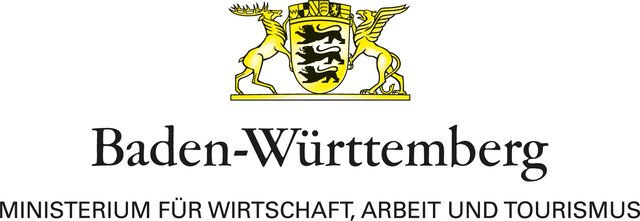
Das Verbundvorhaben “Elektrolyse made in Baden-Württemberg” wurde vom Ministerium für Wirtschaft, Arbeit und Tourismus Baden-Württemberg mit insgesamt 5 Mio. Euro gefördert.
Als Elektrodenpackage (ELP) bezeichnet man die Einheit aus Anode, Bipolarplatte und Kathode. Die Kontaktierung der drei Bleche kann lose (z.B. über Metallnetze) oder formschlüssig (z.B. durch Verschweißen) erfolgen. Elektrodenpackage und Membran werden bei der Stackmontage abwechselnd aufeinandergestapelt und dichten die Halbzellräume gasdicht gegeneinander ab. Dabei werden hohe Anforderungen an die Fertigungstoleranzen des ELPs gestellt, damit die Abdichtung gegen den Zellrahmen zuverlässig erfolgt und die Membran nicht lokal belastet und ggf. beschädigt wird. Mit Blick auf die Serientauglichkeit des ELP-Design spielt die Abfolge der ELP-Fertigungsschritte einschließlich der Beschichtung der Elektroden eine entscheidende Rolle.
Am ZSW wurde ein ELP-Design entwickelt, das kostengünstig aus Baustahl (DC01) umgesetzt und mittels integrierter Stromübertrager formschlüssig verbunden wurde. Hierfür wurden Näpfe als Stromübertrager aus der Elektrodenfläche ausgestellt und mit der Bipolarplatte verschweißt. Während als Anode vernickelter Stahl verwendet wurde, wurde die Kathodenseite des fertigen ELPs abschließend beschichtet. Im Projekt erfolgte dies mit einer Nickel-Aluminium-Molybdän-Schicht (NiAlMo), die mit dem Atmosphärischen Plasmasprayverfahren bei einem Industriepartner (Sybabo) aufgebracht wurde.
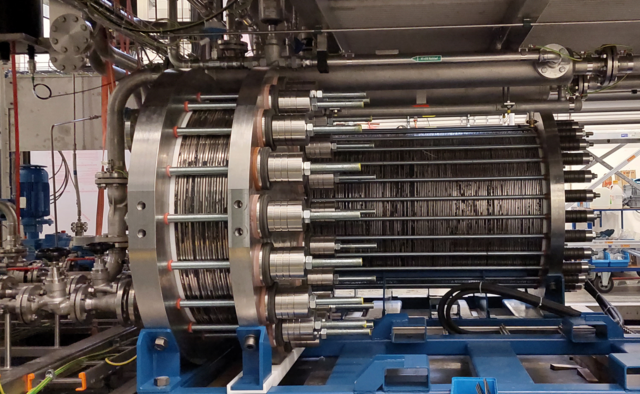
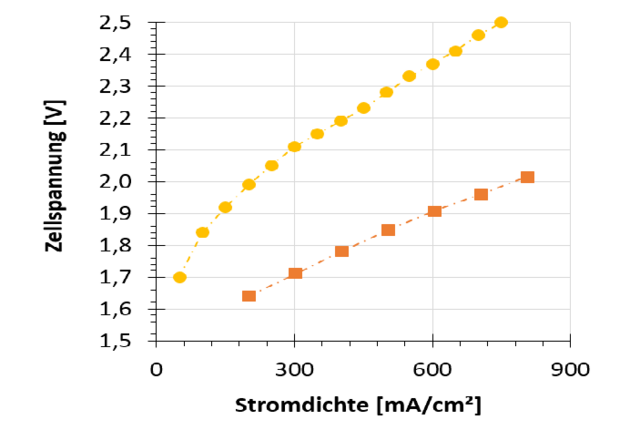
Alkalische Elektrolyseure (AEL) werden heutzutage noch bei vergleichsweise kleiner spezifischer Elektrolyseleistung betrieben, die von der Stromdichte des Elektrolysestacks limitiert wird. Typische Nennstromdichten liegen mit 400 – 600 mA/cm² deutlich unterhalb von denen der sauren Elektrolyse (PEM). Somit wird für dieselbe Produktmenge an Wasserstoff mehr Elektrodenfläche benötigt, was sich in größeren Elektrolyseblöcken bzw. einer höheren Anzahl an Elektrolyseanlagen widerspiegelt.
Daher lag das Hauptaugenmerk am DLR in Stuttgart auf der Entwicklung hocheffizienter Elektrodenbeschichtungen, um die Überspannung von Anode und Kathode zu minimieren und somit höhere Stromdichten beim AEL-Betrieb zu ermöglichen. Mit Blick auf die Ressourcenknappheit kamen hierbei keine Edelmetalle zum Einsatz, sondern Raney-Nickel, das im Fall der Kathode zusätzlich mit Molybdän als katalytisch aktive Komponente dotiert wurde. Für industrielle Anwendungen ist es essentiell, dass sich diese katalytisch aktiven Schichten durch eine hohe Langzeitstabilität auszeichnen. Erst dann können Elektrolyseeffizienz und Wirtschaftlichkeit für die großtechnische Wasserstoffproduktion nachhaltig verbessert werden.
Für die Beschichtung wandte das DLR das atmosphärische Plasmasprayverfahren (APS) an, das hinsichtlich Serienfertigung Zeit- und Kostenvorteile gegenüber dem Vakuumverfahren (VPS) aufweist. Ein Aspekt bei der Optimierung der Beschichtungsparameter lag auf der Reduzierung thermischer und mechanischer Spannungen, die zum Verzug der Elektrode führen können. Vor der Beschichtung wurden die Nickel-Lochbleche sandgestrahlt, um die Oberfläche zu aktivieren und die Schichthaftung zu verbessern. Bei der APS-Beschichtung wird das Pulver der gewünschten Metalllegierung allgemein in den Plasmastrahl eingedüst, sodass die Metallpartikel aufschmelzen, mit hoher Geschwindigkeit auf das Elektrodensubstrat aufprellen und dort zu einer Elektrodenbeschichtung verfestigen. Für die Erzeugung von Raney-Nickel wird die Elektrode üblicherweise in KOH bei Temperaturen von 80°C aktiviert, wobei Aluminium aus der Schicht ausgelaugt wird und die gewünschte hochporöse Nickel-Schicht entsteht. Die nun einsatzbereiten Elektroden wurden sowohl in der Becherglasmesszelle umfangreich elektrochemisch untersucht als auch im AEL-Stack am DLR sowie am ZSW im Dauerbetrieb erprobt. Dabei zeigte sich eine signifikante Verbesserung der Zellspannung. Die Veröffentlichung der Ergebnisse in einem Peer-Review-Paper wird derzeit vorbereitet.
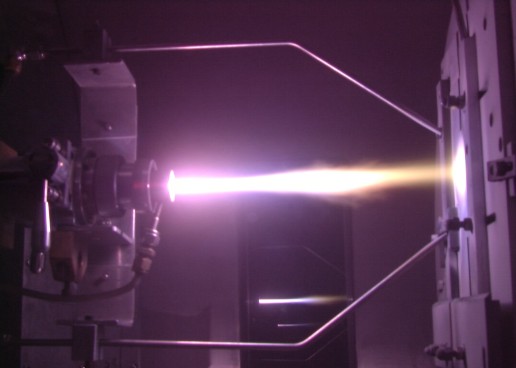
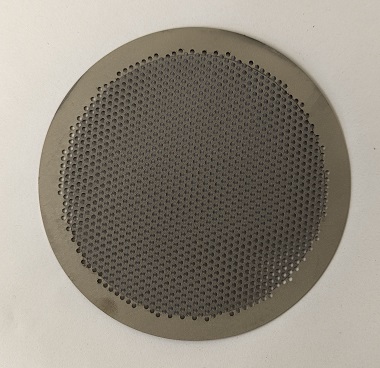
Elektrolysestacks werden derzeit noch als „Black-Box“ betrieben. Das heißt, der Zustand der ein- und ausströmenden Medien des Elektrolysestacks ist zwar bekannt, aber nicht die Betriebsgrößen innerhalb des Stacks oder innerhalb der einzelnen Stackzellen. So bleiben lokale Störungen unentdeckt, bis sie sich zu einem Problem entwickelt haben, das meist zu einem Schaden führt. Daher ist es wichtig, entscheidende Messgrößen wie Temperatur und Zellspannung kontinuierlich zu erfassen. Damit kann der Elektrolysebetrieb überwacht und bei Bedarf angepasst sowie Wartungs- und Reparaturarbeiten genau geplant werden.
Allerdings müssen bei der Umsetzung der stackintegrierten Sensorik einige Hürden genommen werden. Die Belastung auf die verwendeten Materialien innerhalb der Zelle ist höchst anspruchsvoll. So können Temperaturen bis 100°C und Drücke bis 30 bar erreicht werden, während eine turbulente Zweiphasenströmung aus Kalilauge (Elektrolyt) und Sauerstoff bzw. Wasserstoff auf das Material wirkt. Außerdem muss die Datenleitung aus der Zelle durch den Zellrahmen herausgeführt werden, was einen hohen Anspruch an die Stackmontage, die Dichtheit sowie die Robustheit stellt. Außen am Stack ist die Messdatenerfassung angebracht, die ebenfalls Ex-geschützt ausgeführt werden muss.
Am Hahn-Schickard-Institut (HS) in Stuttgart wurden ultradünne Folienschaltungsträger entwickelt, die Sensoren in Dünnschichttechnik oder als SMD-Komponenten aufweisen. Diese wurden auf der Bipolarplatte (Fläche 100cm2) aufgebracht und zum Schutz vor Kalilauge mit einem Verguss verkapselt. Die Spannungs- und Temperatursignale wurden zu einer potentialgetrennten Elektronik geführt, den sogenannten CellNodes, die parallel zu den Elektrolysezellen gestapelt wurden. Final bildete eine BlockHost-Elektronik die Brücke zwischen den gestapelten CellNodes und einem Computer zur Messdatenauswertung. Das Gesamtsystem funktioniert in Wasser sehr gut. Unter AEL-Bedingungen erwies sich der Verguss nicht als ausreichend KOH-beständig, sodass bei der zukünftigen Entwicklung im Rahmen des Anschlussprojektes ElySmartStack ein neues Materialkonzept eingesetzt werden soll.
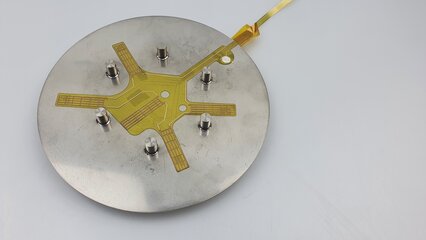
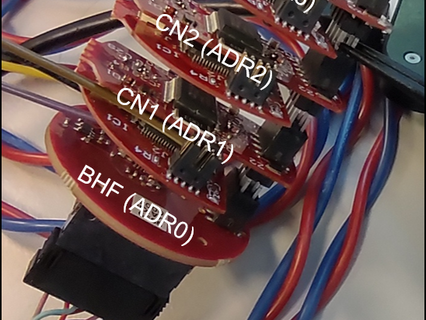
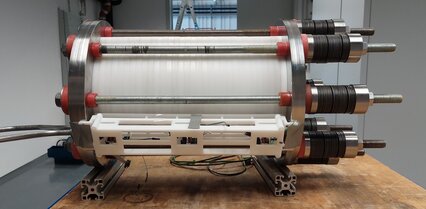
Zur Trennung der beiden Produktgasströme H2 und O2 werden in einer alkalischen Elektrolysezelle Membranen zwischen Anode und Kathode eingesetzt, die die Leitung von OH--Ionen ermöglichen. Dabei verbessert sich der Wirkungsgrad der Zelle, je geringer das Überpotenzial an den Elektroden und je kleiner der ohmsche Widerstand sind. Letzterer wird kleiner und somit günstiger, je kürzer der Elektrodenabstand, je dünner die Membran und je höher die elektrische Leitfähigkeit von Elektrolyt, Membran und Elektrodenpackage sind.
An den DITF in Denkendorf liegt der Fokus auf der Entwicklung faserverstärkter Membranen mit einer möglichst hohen Ionenleitfähigkeit und geringen Dicke bei guter Gasdichtigkeit. Als Stützmaterial wird Feinstfaservlies statt Gewebe eingesetzt, das durch einfachere Technologien mit hoher Produktiongsgeschwindigkeit sehr dünn hergestellt werden kann. Die DITF haben hierfür unter anderem das schmelzebasierte Meltblow-Verfahren genutzt und Vliesstoffe aus PEEK (Polyetheretherketon) mit einem mittleren Faserdurchmesser von 2,0 – 2,5 µm und einem Flächengewicht von ca. 10 g/m² hergestellt. Durch anschließendes Thermokalandrieren konnten die Homogenität der Vliesdicke sowie die maximale Zugkraft verbessert werden.
Im folgenden Prozessschritt haben die DITF die Membran aufgebracht, indem das Vlies mit einer Polymerlösung berakelt wurde, um die Poren des Verstärkungsvlieses mit ionenleitfähigem Matrixpolymerzu füllen und gasdicht zu verschließen. Dabei erwies sich Polybenzimidazol (PBI) als geeignetes Polymer für die Membran. DITF optimierte die einzelnen Prozessschritte mit Fokus auf die Membraneigenschaften Ionenleitfähigkeit, Dicke, Gasdichtigkeit, Zugkraft und Homogenität. Abschließend erfolgte die Charakterisierung vorausgewählter Membranen in der Becherglasmesszelle am DLR und schließlich die Erprobung der neuen PBI-Membran mit PEEK-Vliesverstärkung im AEL-Stack am ZSW. Dabei wurden sehr gute Zellspannung nachgewiesen und die Gasqualität lag trotz der geringen Membrandicke (< 50 µm) im Bereich deutlich dickerer, kommerzieller Membranen.
Ansprechpartner bei den Forschungsinstituten
Zentrum für Sonnenenergie-
und Wasserstoff-Forschung
Fachgebiet Regenerative
Energieträger und Verfahren
Bernd Stürmer
bernd.stuermer(at)zsw-bw.de
Deutsches Zentrum für Luft-
und Raumfahrt (DLR)
Institut für Technische Thermodynamik
Energiesystemintegration
Syed-Asif Ansar
syed-asif.ansar(at)dlr.de
Hahn-Schickard-Gesellschaft für
angewandte Forschung e.V.
Dr.-Ing. Florian Janek
florian.janek(at)hahn-schickard.de
Deutsche Institute für Textil- und
Faserforschung Denkendorf (DITF)
Dr. rer. nat. Hagen J. Altmann
hagen.altmann(at)ditf.de
Simon Ringger M.Sc.
simon.ringger(at)ditf.de